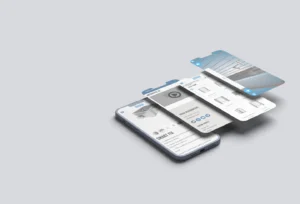
INTERACTIVE ASSEMBLY INSTRUCTIONS
Step-by-step assembly guidance that brings efficiency and ease to every installation.
GET STARTED HEREStep-by-step assembly guidance that brings efficiency and ease to every installation.
GET STARTED HERETroax offers durable, customizable mesh enclosures to protect server racks from unauthorized access. Our solutions secure your data centre by providing robust physical protection against tampering
Safety Solutions for a Secure Workplace
Troax solves its customers safety challenges with highly durable, flexible, and innovative safety solutions. Every day, the vision of a safer workplace drives us to deliver excellence. We build on strong partnerships that encompass everything from initial consultation to implementation and ongoing support. In every project, Troax ensures the highest standards of safety and efficiency, protecting both people and processes.
DRAW YOUR LAYOUT WITH OUR DESIGN TOOL
Create, preview, and order custom Machine Guarding solutions